The Science Behind Porosity: A Comprehensive Overview for Welders and Fabricators
Understanding the elaborate devices behind porosity in welding is essential for welders and producers making every effort for impeccable workmanship. From the make-up of the base materials to the details of the welding procedure itself, a wide range of variables conspire to either intensify or reduce the visibility of porosity.
Comprehending Porosity in Welding
FIRST SENTENCE:
Evaluation of porosity in welding exposes important insights right into the stability and high quality of the weld joint. Porosity, identified by the visibility of dental caries or spaces within the weld steel, is a typical concern in welding processes. These spaces, otherwise correctly dealt with, can compromise the structural stability and mechanical properties of the weld, resulting in potential failings in the ended up item.
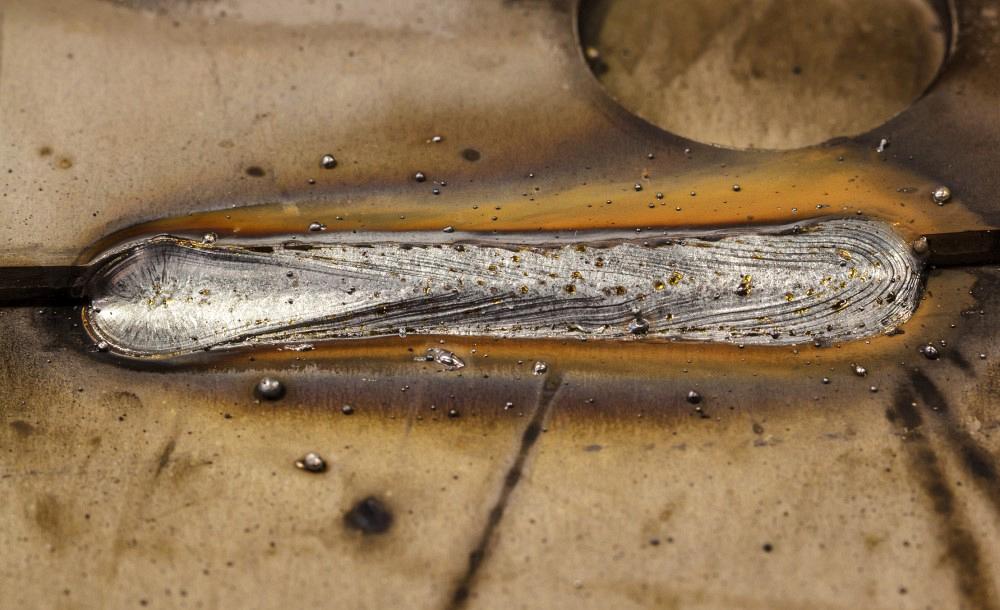
To discover and evaluate porosity, non-destructive testing techniques such as ultrasonic testing or X-ray inspection are usually utilized. These techniques enable the identification of inner flaws without endangering the stability of the weld. By assessing the dimension, form, and circulation of porosity within a weld, welders can make enlightened choices to enhance their welding procedures and achieve sounder weld joints.
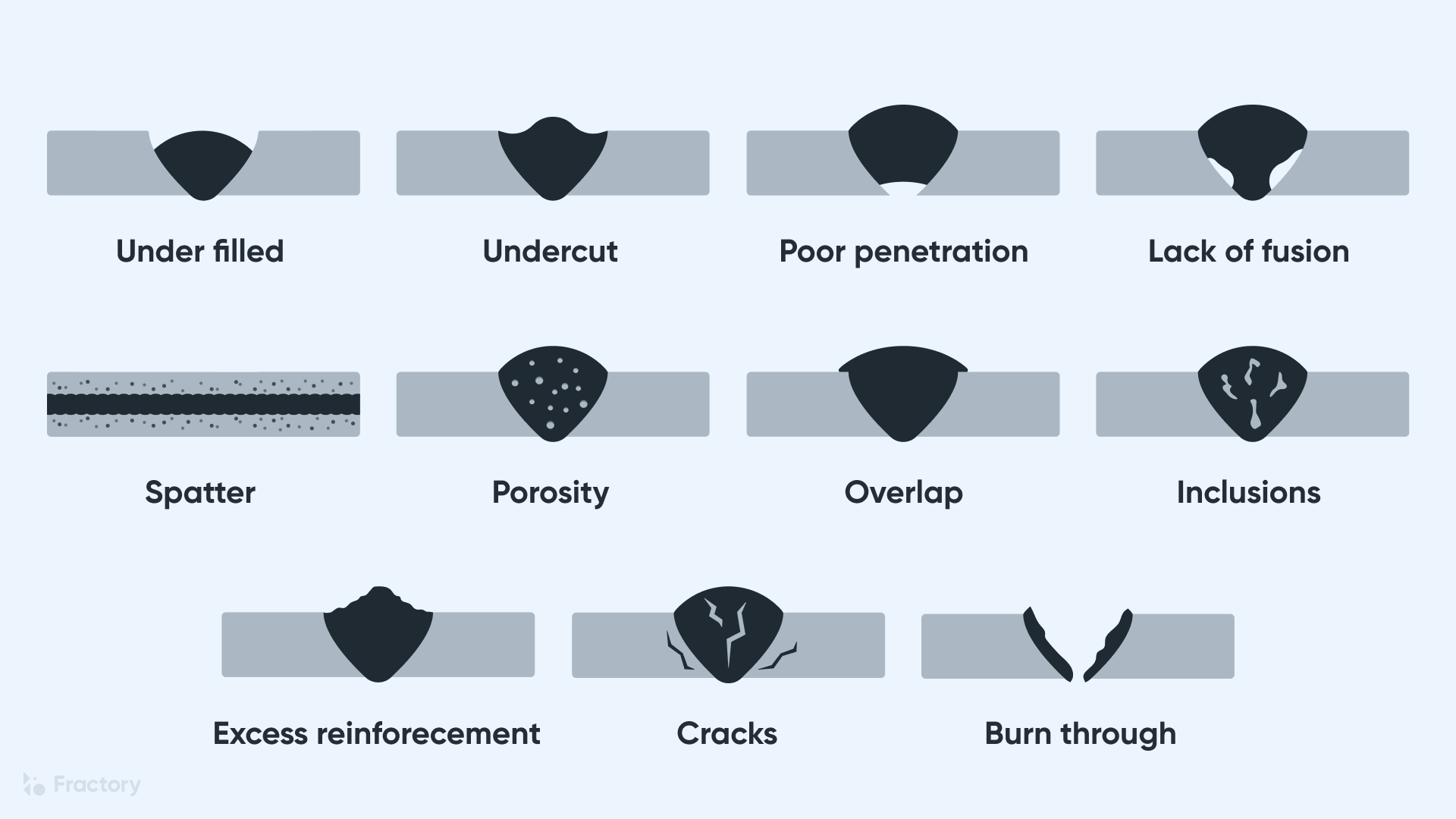
Variables Affecting Porosity Development
The occurrence of porosity in welding is influenced by a myriad of factors, ranging from gas securing performance to the complexities of welding specification settings. Welding parameters, including voltage, current, travel rate, and electrode type, likewise influence porosity formation. The welding technique used, such as gas metal arc welding (GMAW) or shielded metal arc welding (SMAW), can influence porosity development due to variants in warmth distribution and gas protection - What is Porosity.
Impacts of Porosity on Weld Top Quality
Porosity development significantly endangers the structural integrity and mechanical buildings of welded joints. When porosity exists in a weld, it creates voids or cavities within the material, lowering the general her response toughness of the joint. These gaps function as stress and anxiety concentration factors, making the weld more vulnerable to splitting and failing under tons. The visibility of porosity additionally damages the weld's resistance to deterioration, as the entraped air or gases within deep spaces can respond with the surrounding environment, resulting in deterioration in time. Furthermore, porosity can prevent the weld's capability to withstand pressure or influence, additional endangering the overall top quality and reliability of the bonded framework. In vital applications such as aerospace, automobile, or architectural constructions, where safety and security and durability are paramount, the harmful results of porosity on weld top quality can have extreme consequences, emphasizing the significance of minimizing porosity with appropriate welding strategies and procedures.
Strategies to Decrease Porosity
Furthermore, making use of the appropriate welding criteria, such as the proper voltage, existing, and take a trip rate, is this link vital in preventing porosity. Keeping a regular arc size and angle throughout welding likewise helps decrease the chance of porosity.

Utilizing the appropriate welding strategy, such as back-stepping or employing a weaving movement, can also help distribute warmth equally and decrease the chances of porosity formation. By implementing these techniques, welders can effectively lessen porosity and generate high-grade welded joints.
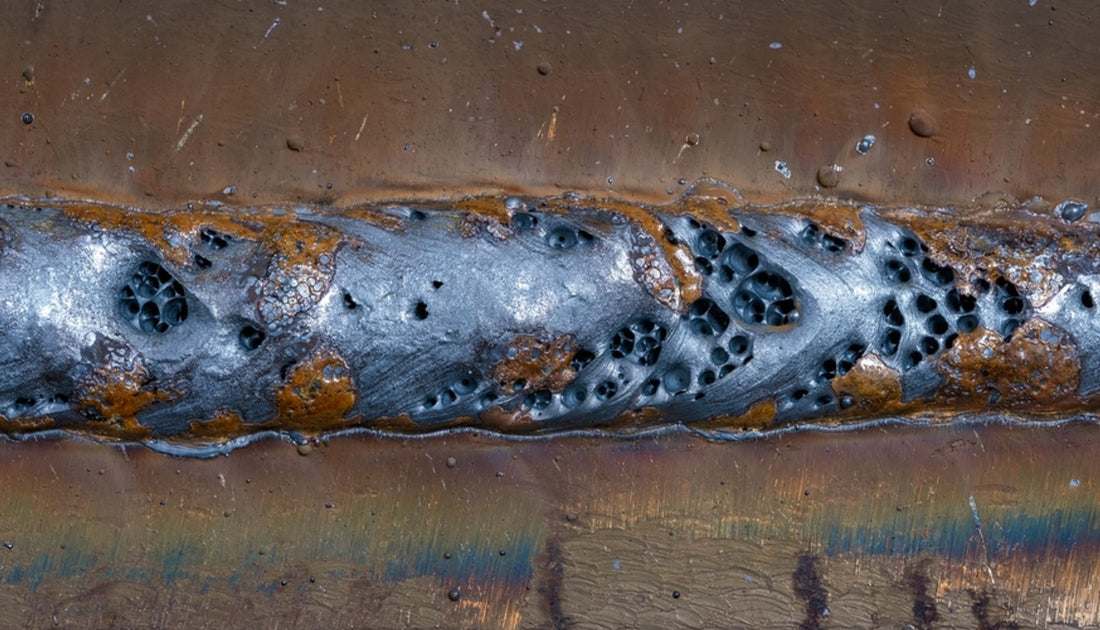
Advanced Solutions for Porosity Control
Applying advanced modern technologies and cutting-edge approaches plays a crucial function in attaining superior control over porosity in welding procedures. In addition, employing advanced welding strategies such as pulsed MIG welding or customized ambience welding can likewise assist reduce porosity issues.
Another innovative remedy involves making use of innovative welding equipment. Making use of equipment with built-in attributes like waveform control and sophisticated power resources can boost weld quality and lower porosity risks. The execution of automated welding systems with precise control over parameters can dramatically lessen porosity defects.
Furthermore, integrating innovative surveillance and evaluation modern technologies such as real-time X-ray imaging or automated ultrasonic screening can help in identifying porosity early in the welding procedure, enabling prompt corrective activities. On the whole, incorporating these sophisticated Continue options can greatly enhance porosity control and boost the general top quality of welded elements.
Verdict
Finally, recognizing the scientific research behind porosity in welding is essential for welders and makers to produce top notch welds. By identifying the elements affecting porosity development and applying strategies to minimize it, welders can boost the total weld high quality. Advanced services for porosity control can additionally boost the welding procedure and make sure a solid and reputable weld. It is very important for welders to continually enlighten themselves on porosity and apply best methods to achieve optimal results.